The art of the goldsmith
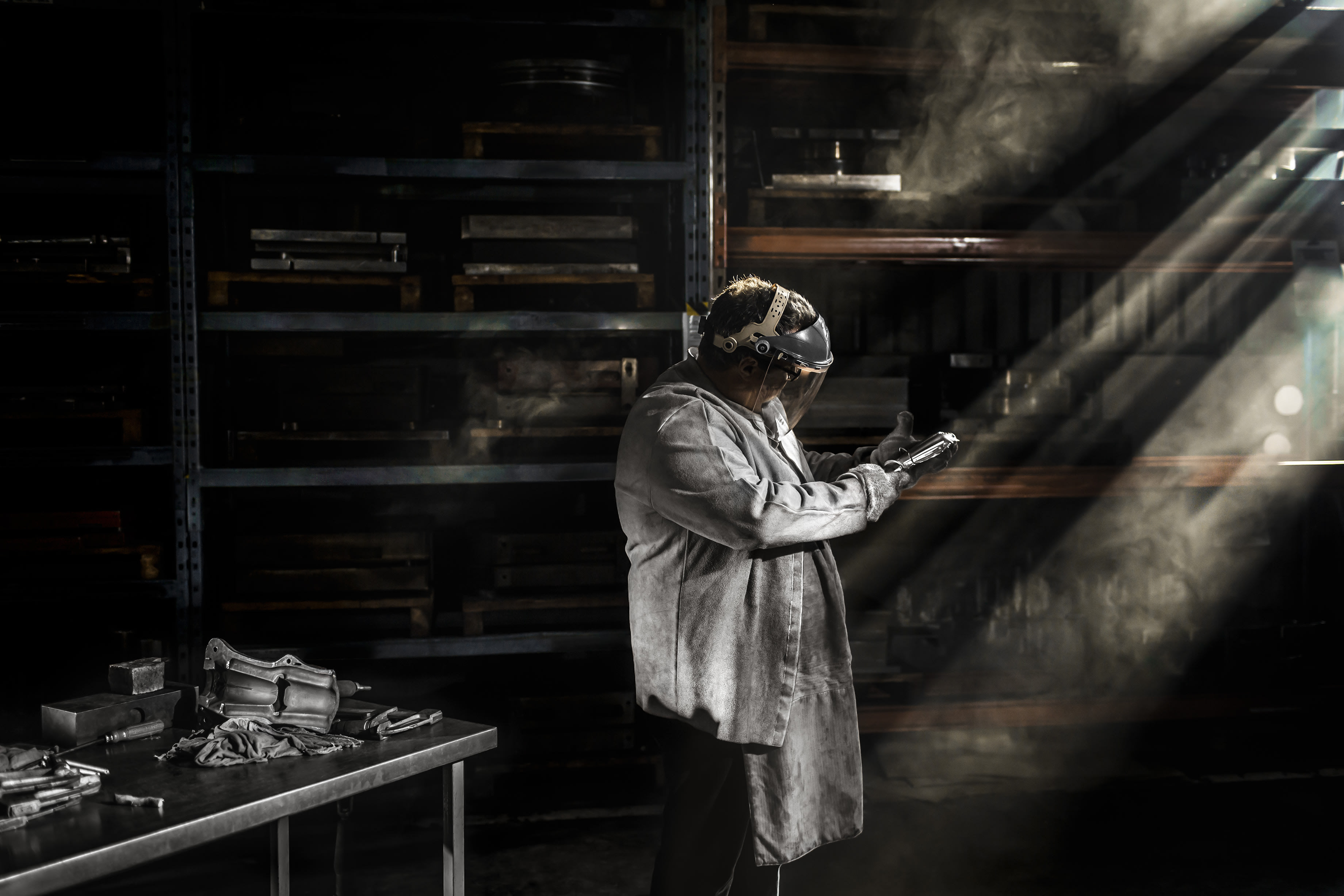
A goldsmith's work
Goldsmithing designates both a profession, practiced since ancient times, and all works made of precious metal, as well as silver and gold. Jewelry, medals and coins are no longer part of the jewelry.
During the 18th century, the market was divided into two major specialties: the small goldsmith's, including cutlery and small works, and the big goldsmith.
Taking advantage of the malleability and ductility of precious metals, the goldsmith uses several techniques to shape and decorate the metal.
Formatting
Traditionally, it is done at a cold temperature, interspersed with annealing that makes the metal flexible again. The goldsmith always begins its shaping from a blank: a flat plate that is cut to the desired dimensions.
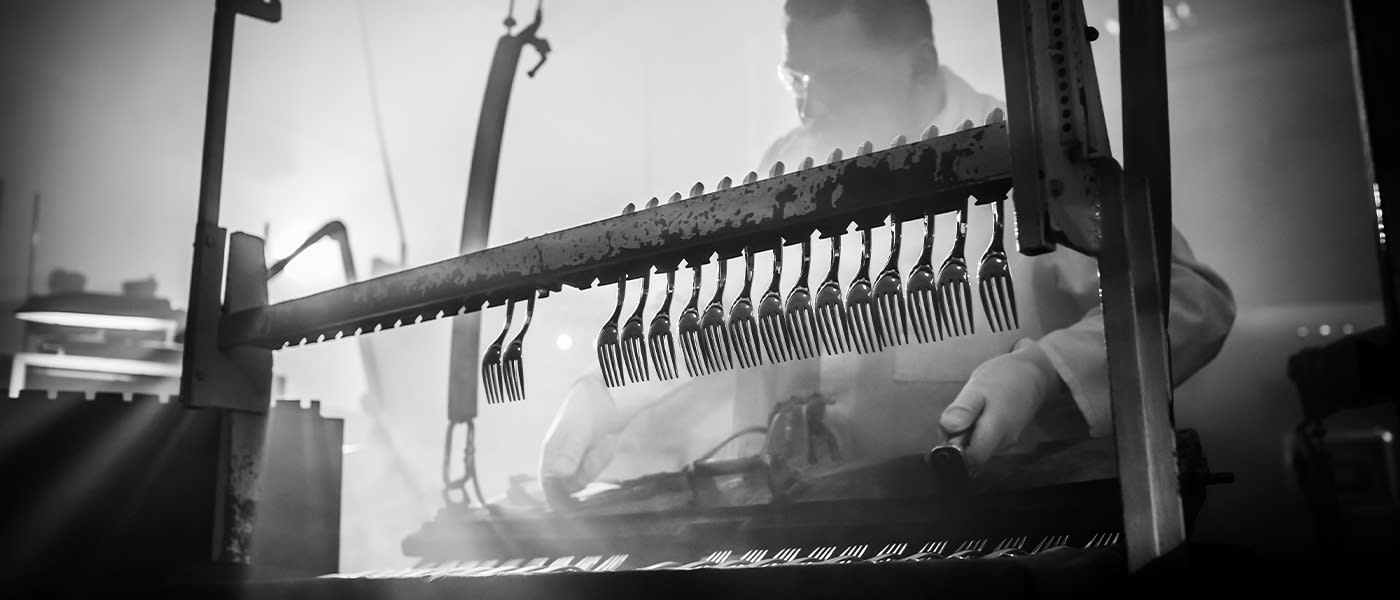
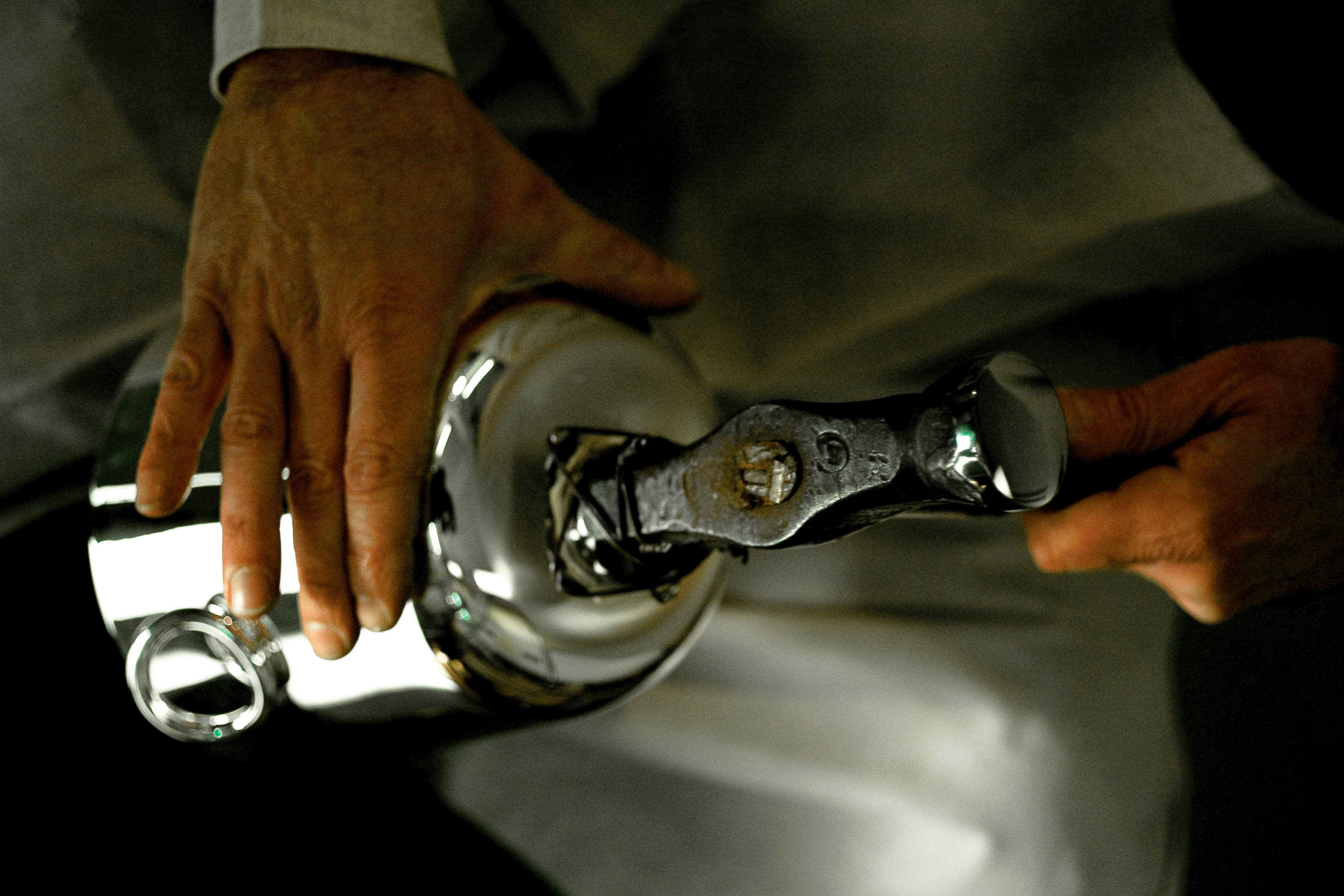
LEVELING
Hammer work is the oldest of these shaping techniques. Using wooden mallets and hammers, the silversmith strikes the metal until it reaches the desired shape. For flat parts, the term used is leveling and the work is done from the inside.
For hollow parts, it is a shrinkage, where the metal is worked from the outside.
In the French tradition, the purpose is a so-called taut finish, where the hammering is not visible on the item.
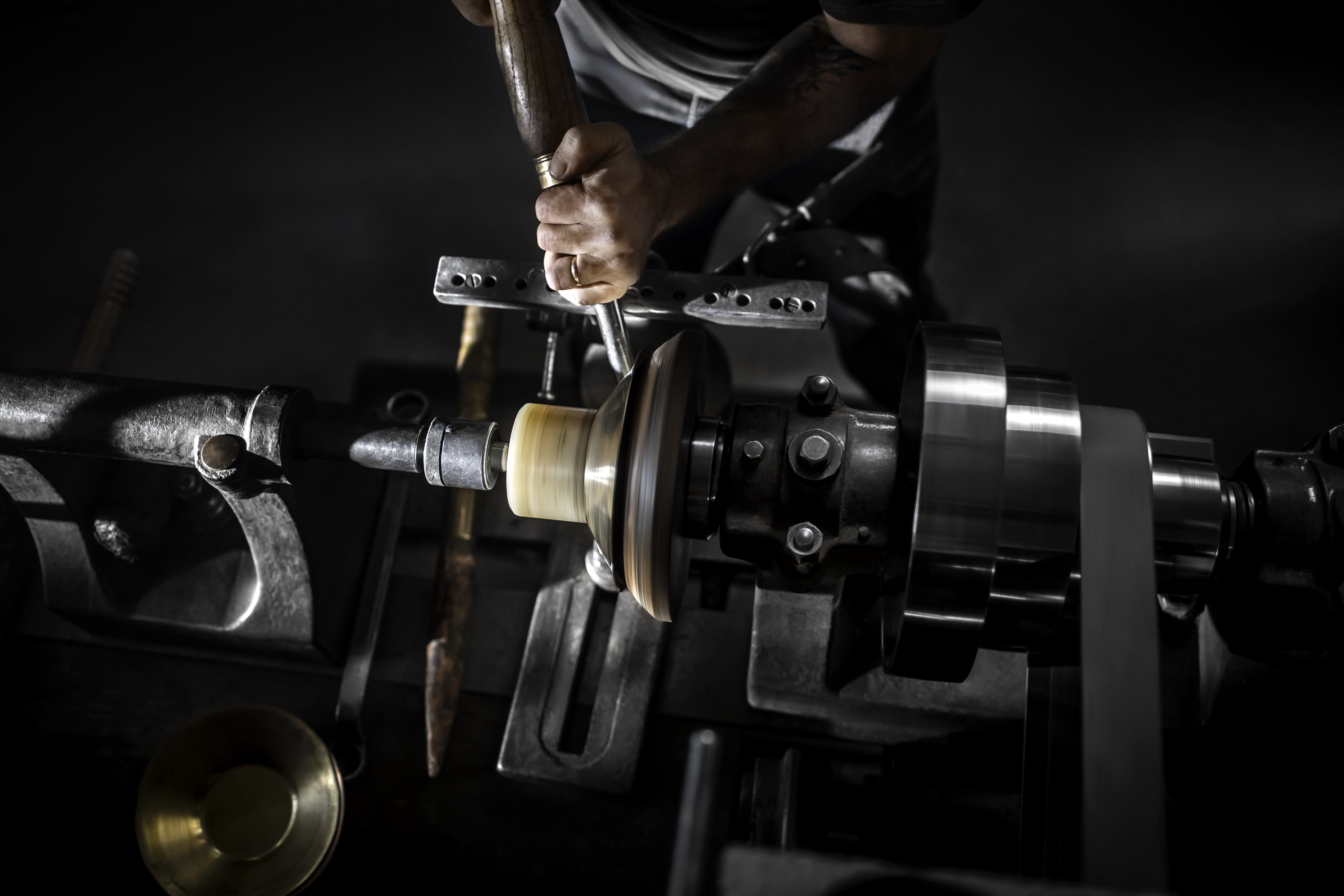
SPINNING SHOOT
The turning-spinning was introduced in France during the 19th century.
First mechanization of hammer work, it allows to manufacture hollow and symmetrical shapes on a mechanical and horizontal lathe. The lather starts by creating the forms, generally made of wood, necessary for the production of the item: "the mandrels". Once the mandrels are made, he will be able to work the metal. He sets and centers the lathe, then the metal blank.
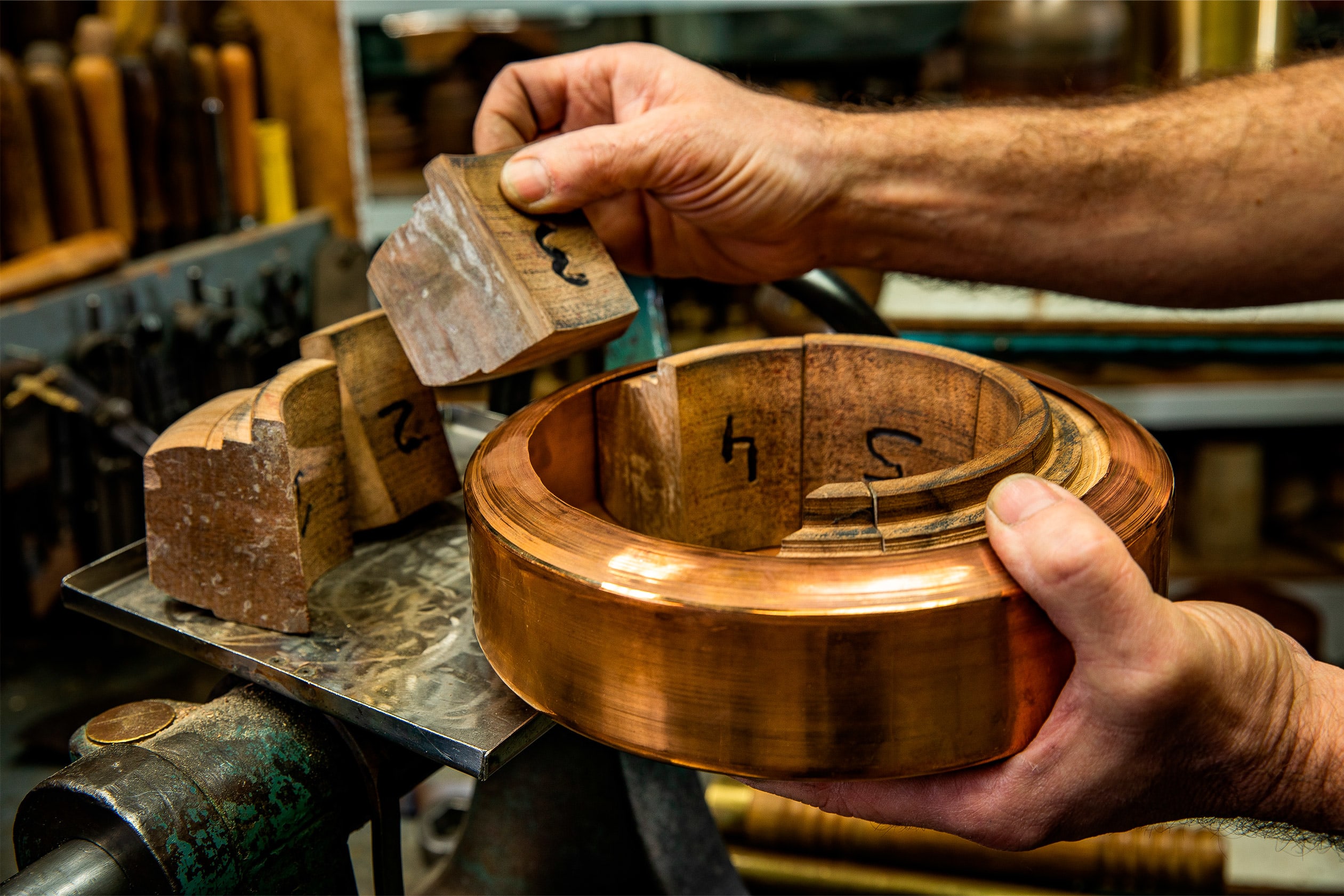
BROKEN CHUCK
When the lathe is rotating, he pushes the metal back onto the mandrel using a tool called a "spoon".
The turner must master the force with which he repels the metal and the time of embossing, otherwise he will break the item or damage the mandrel.
Cast iron, work by casting molten metal, is used for high relief parts and sculptures.
The decor
CHISELLING
Chiselling consists in deforming the metal without taking part of it using a hammer. The chiseler, depending on the chosen chasers, will obtain more or less wide lines.
To obtain a salient pattern, the work is done from the back to the right, the carving is then said to be "En repoussé". It is the chiseller task to resume the casts, to give the decor the nervousness that makes its beauty.
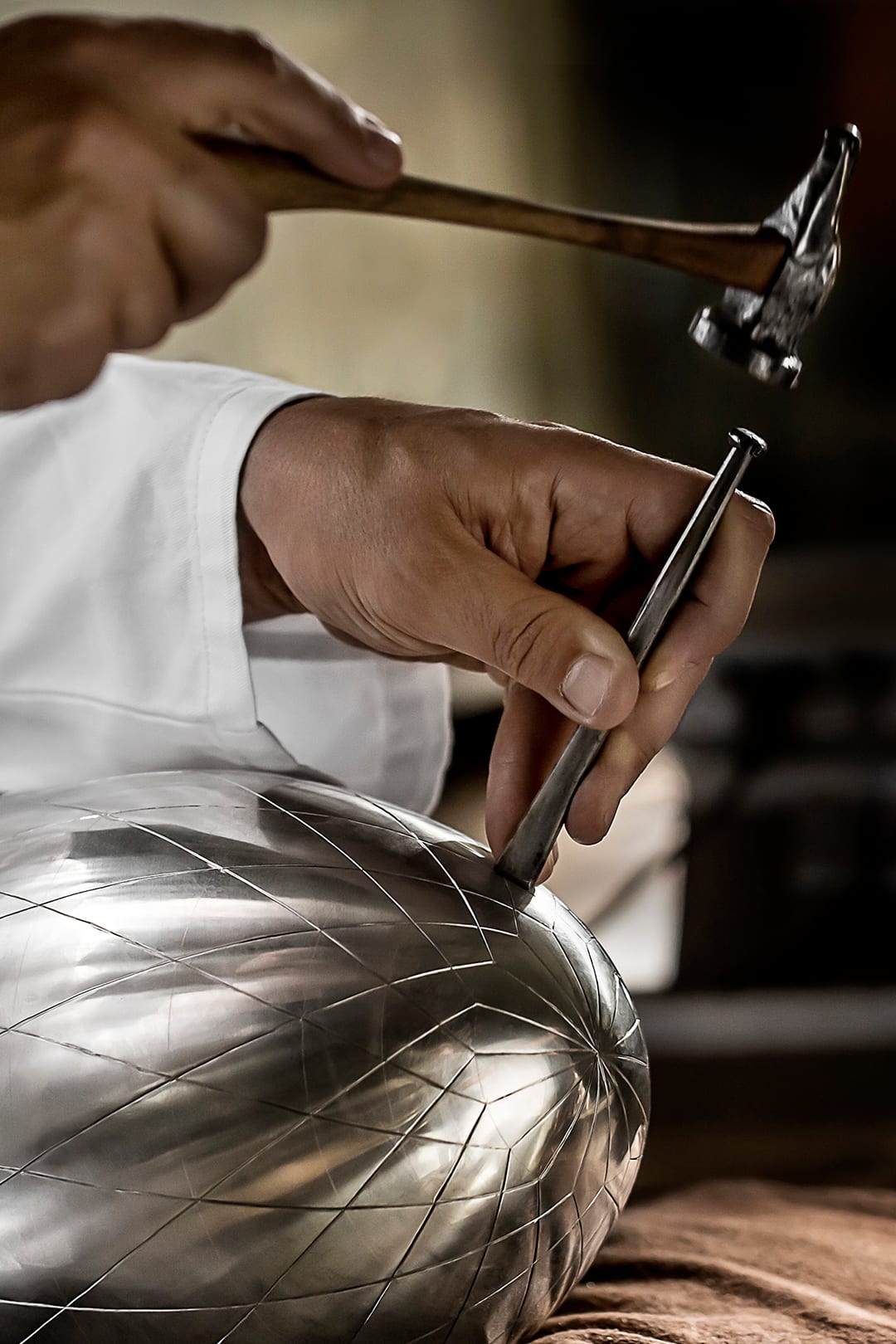
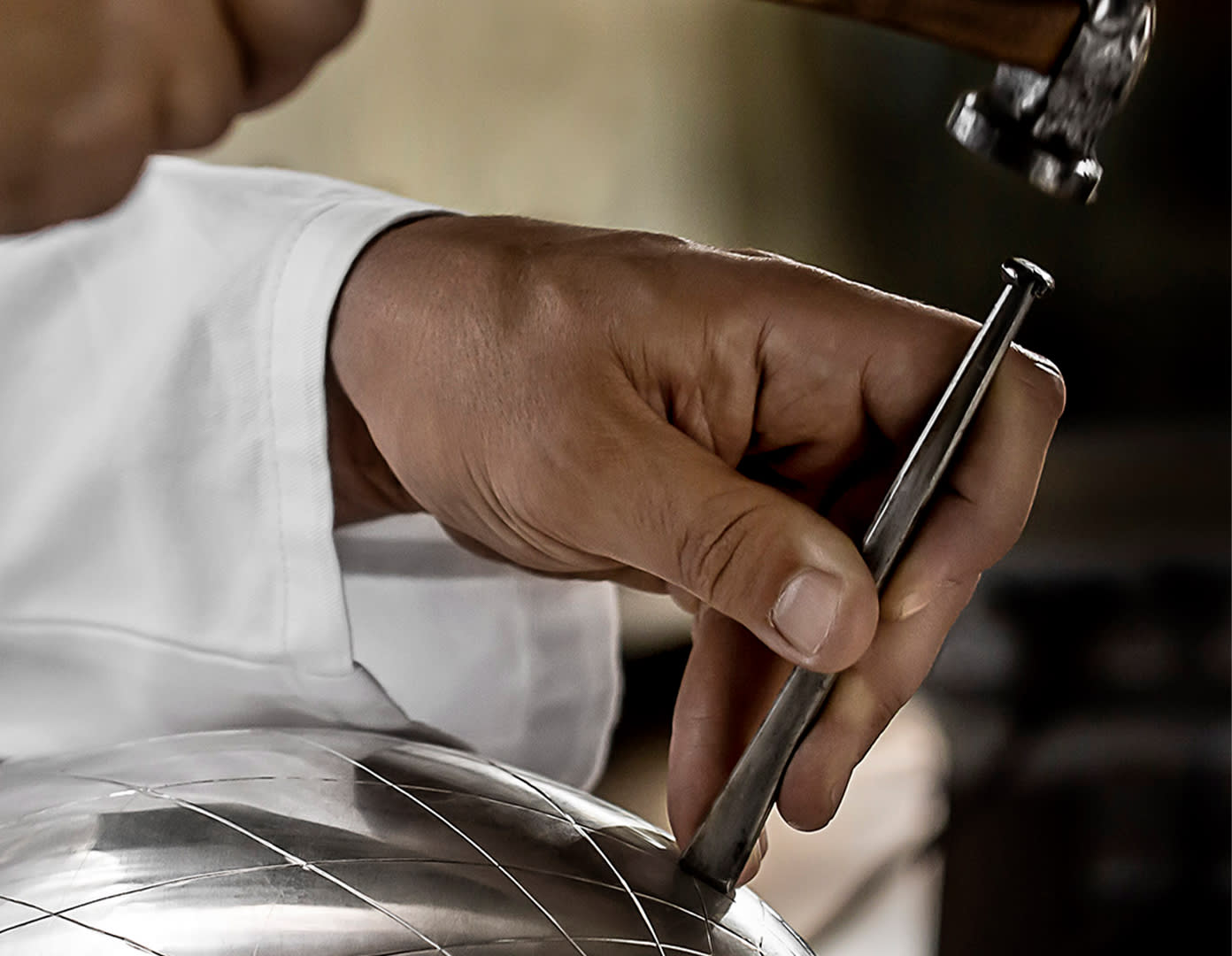
ENGRAVING
Engraving is done by removing a metal groove using a chisel. It is mainly used on finished parts to personalize them.
The item is often made in several parts so it is the job of the goldsmith-assembler to put them together. This step is extremely delicate since the goldsmith tradition only tolerates invisible assemblies.
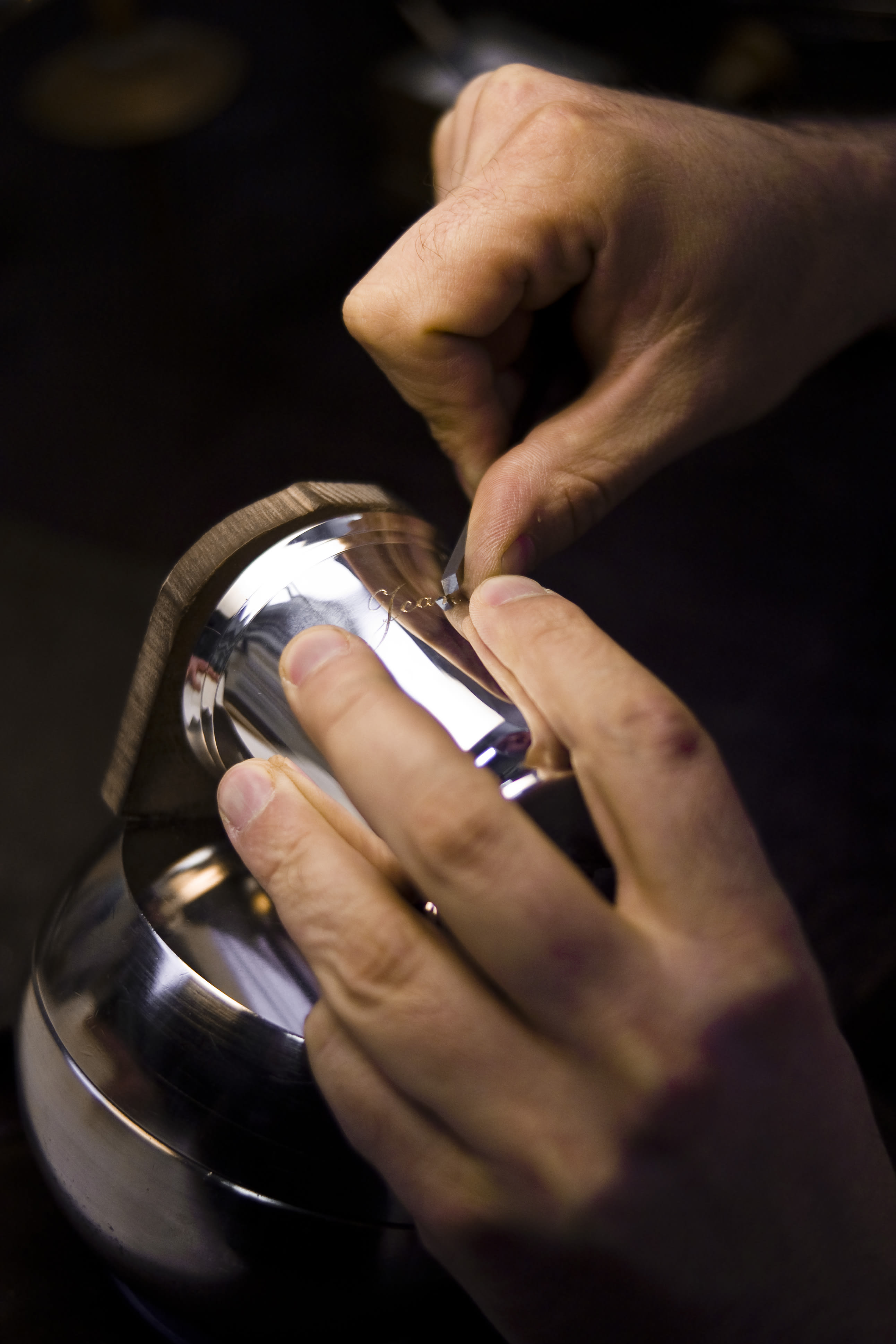
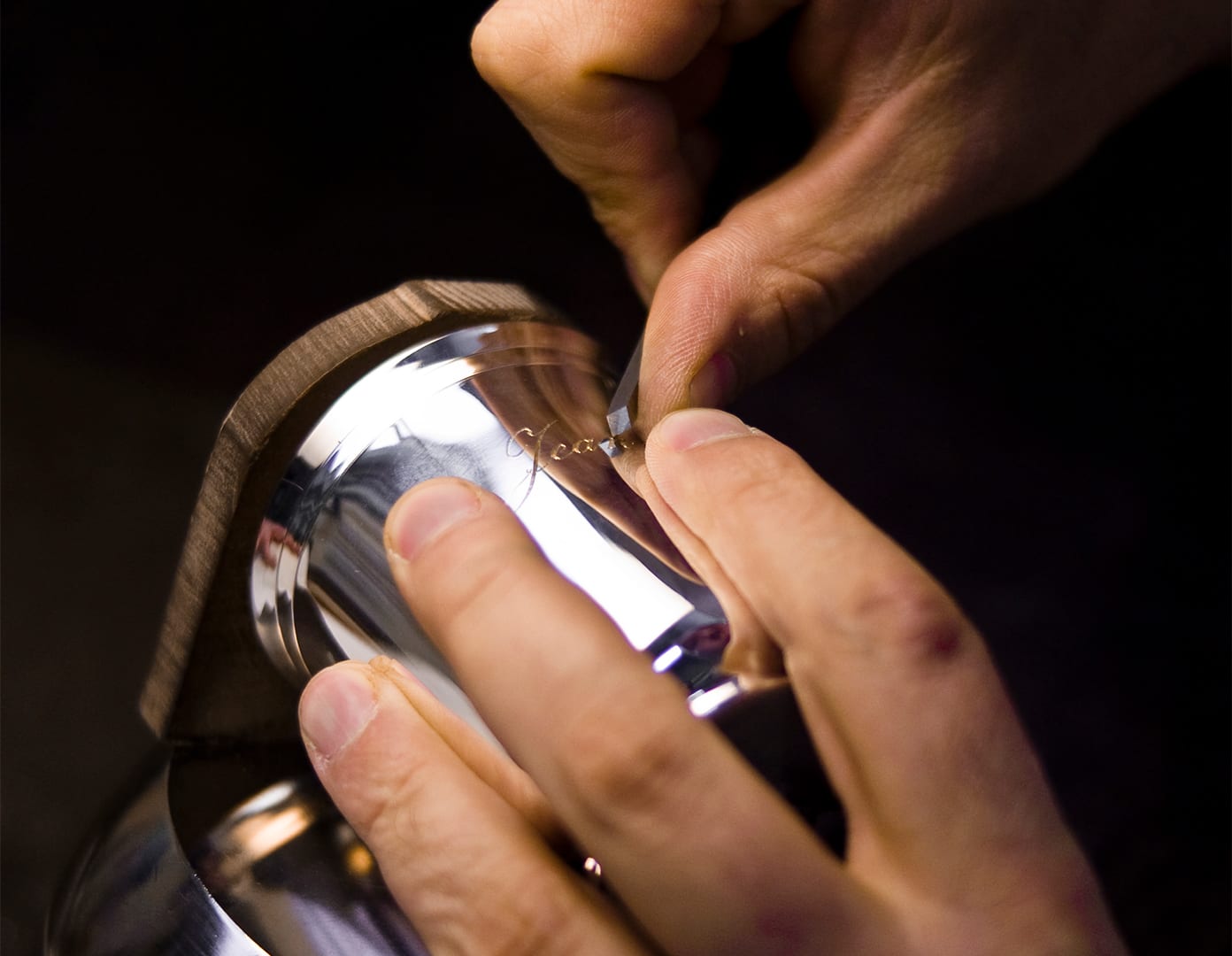
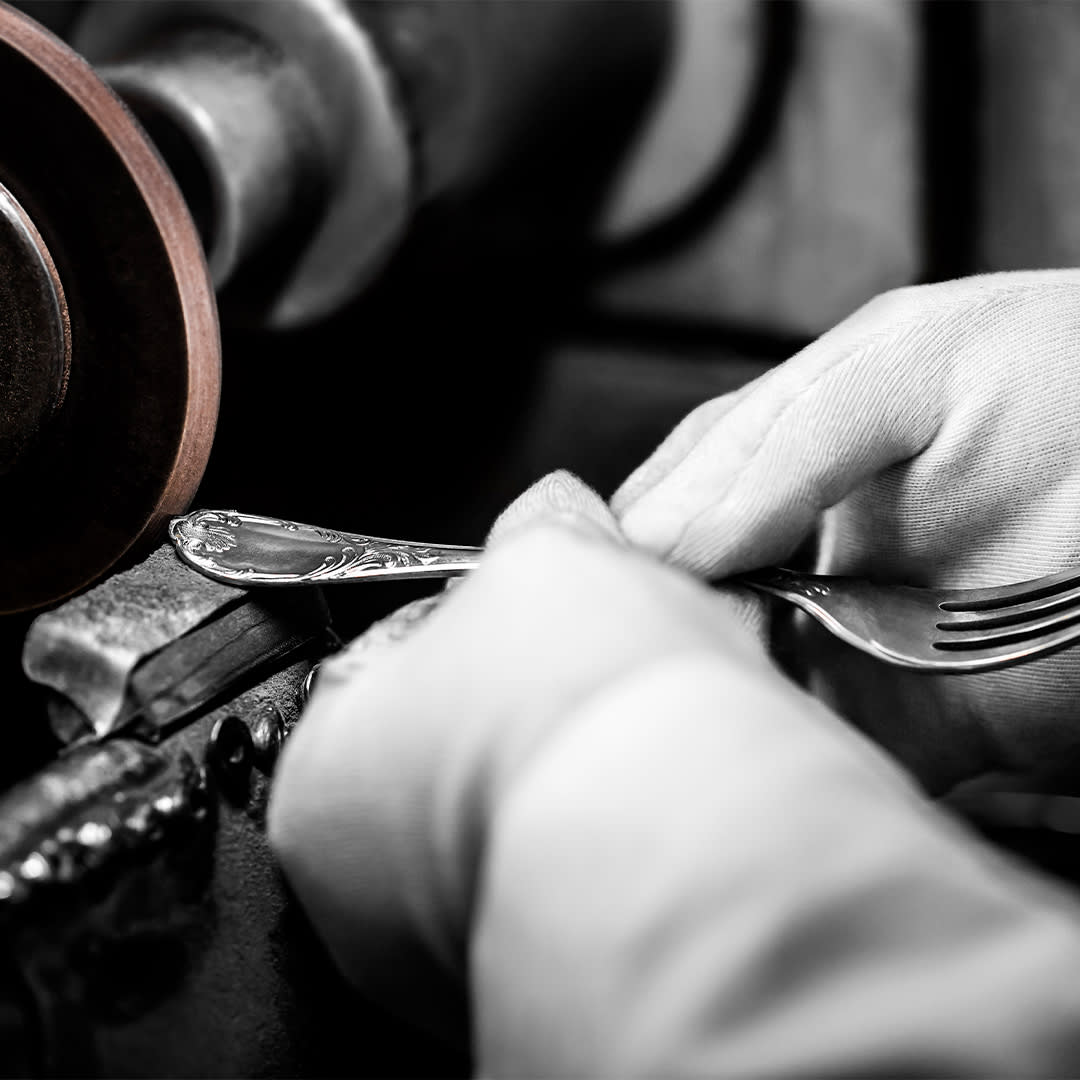
Finishing
Once the item is shaped, decorated, assembled and potentially silvered, is can be polished and sharpened.
Silver or gold items are first polished, before any surface treatment, then brightened after silvering or gilding.
Here are some secrets of goldsmiths revealed. Now it's time to see the beauty of objects that will brighten up, tableware and interiors.
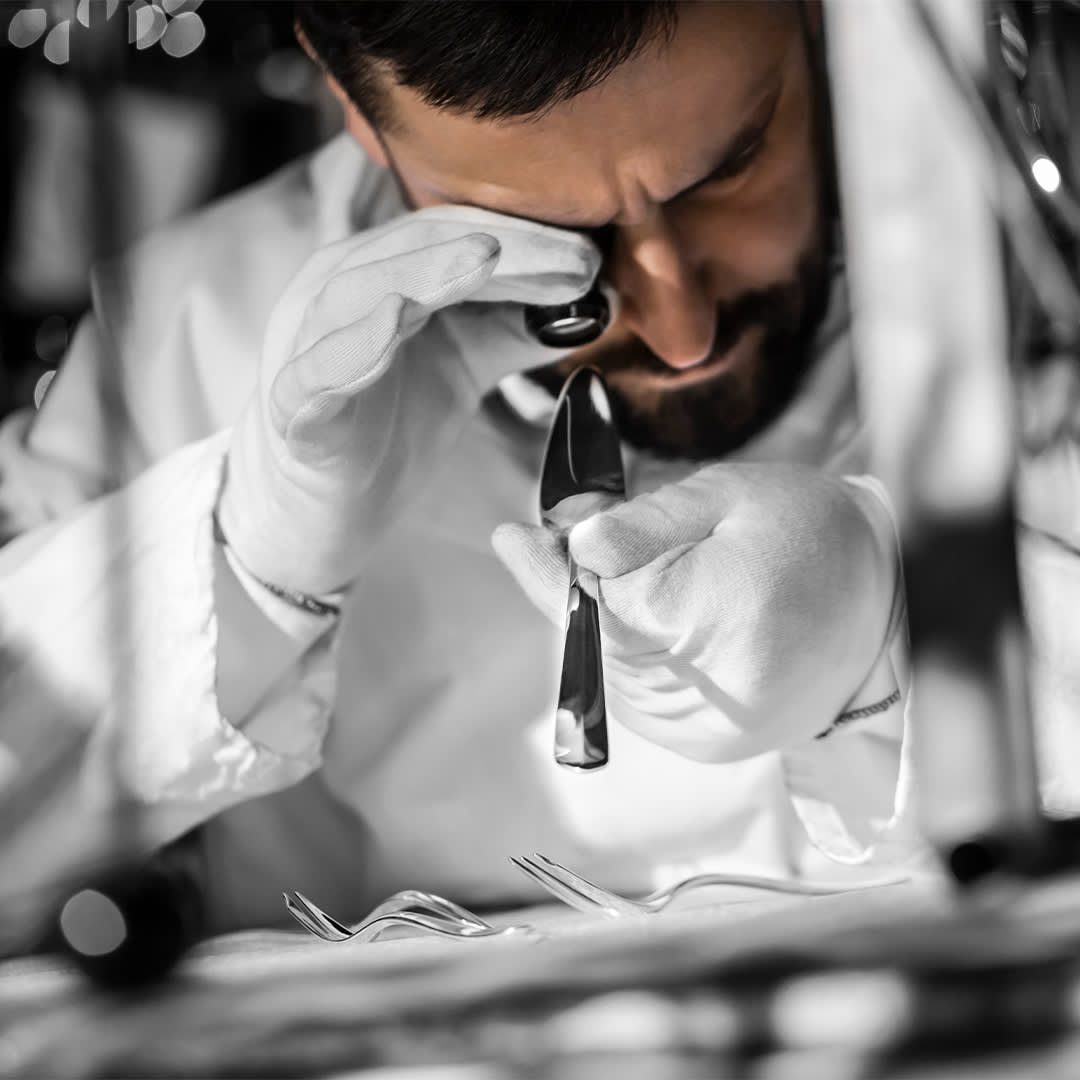